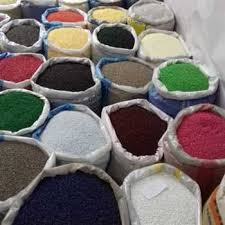
Rubber and plastic are two of the most widely used materials in modern manufacturing, essential in industries ranging from automotive to consumer goods, electronics, and healthcare. Their versatility and durability make them indispensable in countless applications. The key to understanding their properties and performance lies in the raw materials used in their production. In this article, we will explore the primary raw materials for rubber and plastics, focusing on their sources, types, and roles in the final products مواد اولیه لاستیک و پلاستیک.
Understanding Rubber
Rubber is a polymeric material known for its elasticity, resilience, and flexibility. It can be natural or synthetic, and its performance depends largely on the raw materials used in its production. Rubber is utilized in many applications such as tires, seals, gaskets, footwear, and medical devices. The materials involved in the production of rubber are crucial to the properties of the final product.
Natural Rubber
Natural rubber, also known as latex, is derived from the sap of the rubber tree (Hevea brasiliensis). This latex is collected and processed into rubber sheets or other forms suitable for manufacturing. The primary raw material in natural rubber is latex, which is composed of polymers, water, and various other compounds. The quality of natural rubber can vary depending on factors such as the climate in which the rubber trees are grown and the harvesting methods used.
Latex undergoes a process called vulcanization, in which it is heated with sulfur and other additives. This cross-links the polymer chains, increasing the rubber’s strength and elasticity. During vulcanization, the rubber takes on its characteristic properties such as heat resistance and wear resistance. The raw materials involved in this process include sulfur, accelerators, and activators. Sulfur forms cross-links between the polymer chains, while accelerators speed up the vulcanization process, and activators help improve the reaction between sulfur and the rubber.
Synthetic Rubber
Synthetic rubber is produced through the polymerization of various monomers, which are derived from petroleum-based chemicals. The most commonly used types of synthetic rubber are styrene-butadiene rubber (SBR), butyl rubber, and neoprene. These rubbers are made by combining various chemicals in controlled environments to form long-chain polymers.
The key raw materials for synthetic rubber production are monomers such as butadiene, styrene, isoprene, and chloroprene. Butadiene, for example, is a key monomer used to create SBR, which is widely used in tire production due to its durability and performance under varying conditions. The polymerization process can be initiated using a variety of catalysts, and different additives such as stabilizers, plasticizers, and antioxidants are used to enhance the final product’s properties.
Understanding Plastics
Plastics are synthetic materials made from polymers that can be molded into different shapes when heated. These materials are characterized by their ability to be shaped into complex forms, making them ideal for use in a wide variety of applications, from packaging and construction to electronics and medical devices. The production of plastic involves a variety of raw materials that influence the final product’s strength, flexibility, and heat resistance.
Thermoplastics
Thermoplastics are a category of plastics that become soft and moldable when heated and harden upon cooling. This process can be repeated multiple times, making thermoplastics versatile for different manufacturing methods. Common types of thermoplastics include polyethylene (PE), polypropylene (PP), polyvinyl chloride (PVC), and polystyrene (PS).
The raw materials for thermoplastics are primarily monomers that are polymerized into long chains. For example, ethylene is the monomer used to create polyethylene, while propylene is used for polypropylene. Additives such as stabilizers, antioxidants, and colorants are also mixed with the polymer to enhance properties such as UV resistance, flame retardancy, and aesthetic appeal. The specific monomer and additives used can greatly affect the plastic’s properties, such as strength, flexibility, and durability.
Thermosets
Thermosetting plastics, or thermosets, are polymers that undergo an irreversible chemical change when heated and molded. Unlike thermoplastics, thermosets cannot be remolded after they have been set, making them more suitable for high-performance applications. Epoxy, phenolic, and melamine are common types of thermosetting plastics used in a wide range of industries, including aerospace, automotive, and electronics.
The raw materials for thermosets include monomers such as bisphenol-A (for epoxy resins) and formaldehyde (for phenolic resins). These monomers undergo polymerization or condensation reactions in the presence of a catalyst to form rigid networks of polymer chains. The addition of curing agents or hardeners during the manufacturing process ensures that the plastic sets into its final form. Fillers, reinforcements (such as fiberglass), and additives are often mixed into thermosetting plastics to improve their strength, thermal stability, and electrical properties.
Key Raw Materials in Rubber and Plastic Production
Fillers and Reinforcements
Both rubber and plastic production often involves the addition of fillers and reinforcements to improve the material’s properties. Fillers such as carbon black, clay, talc, and silica are commonly added to rubber to enhance strength, wear resistance, and heat resistance. In plastics, fillers like calcium carbonate, glass fibers, and titanium dioxide are used to improve mechanical properties and reduce costs. Reinforcements, particularly in plastics, often include fiberglass and carbon fibers, which increase tensile strength and dimensional stability.
Plasticizers and Additives
To improve the flexibility and processability of rubber and plastics, plasticizers and various additives are used. In rubber, processing oils and plasticizers help reduce viscosity, making the material easier to handle during production. Common plasticizers in rubber include aromatic oils and synthetic plasticizers.
In plastics, plasticizers such as phthalates and adipates are added to reduce the material’s hardness and increase flexibility. Additionally, antioxidants, UV stabilizers, and flame retardants are included in plastic formulations to extend the lifespan and improve safety, particularly in outdoor and electrical applications.
Conclusion
The raw materials for rubber and plastic are critical to the performance and functionality of the final products. From natural and synthetic rubber to the various types of plastics, each material is created by combining a variety of polymers, monomers, fillers, and additives to achieve specific properties. Understanding the role of مواد اولیه لاستیک و پلاستیک is essential for anyone involved in manufacturing or using these materials, as it provides the foundation for the development of advanced products used in everyday life. As technology advances, new raw materials and production techniques will continue to evolve, improving the performance, sustainability, and versatility of rubber and plastic products across all industries.